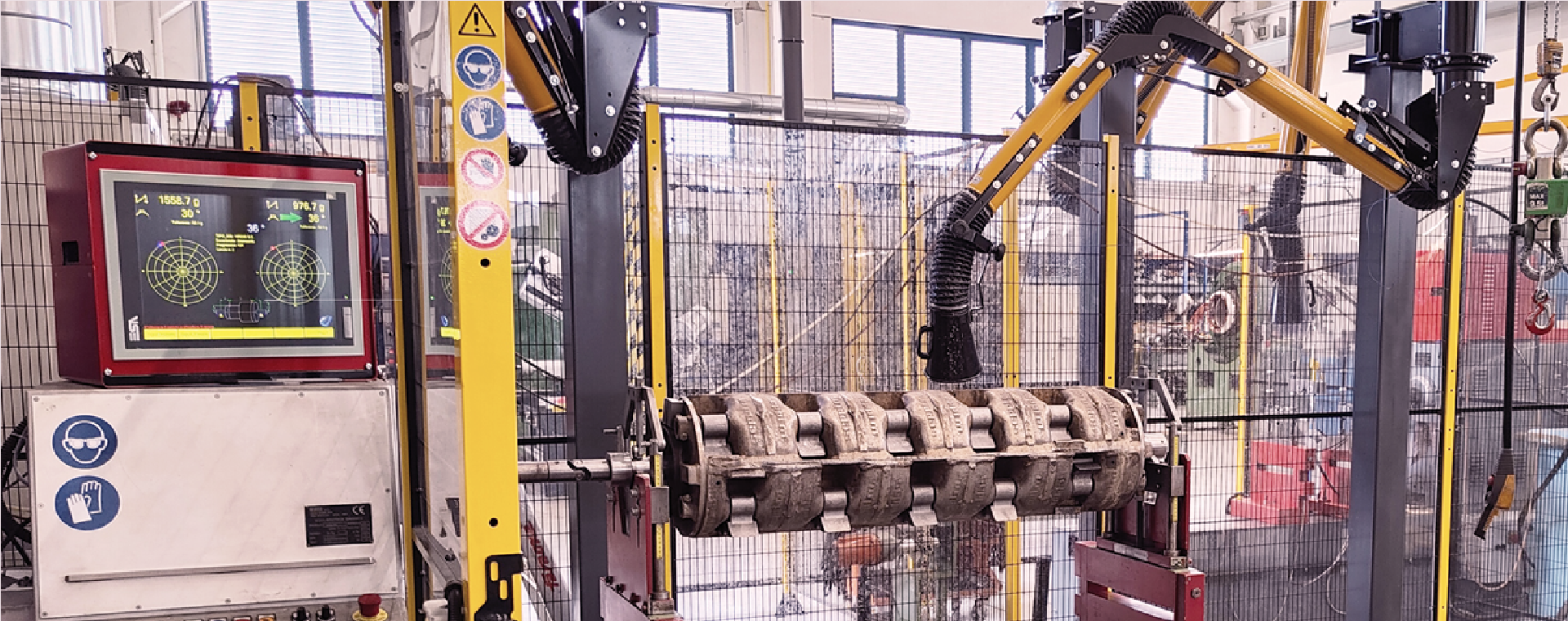
6 April 2023
Maschietto and workshop 4.0: a success story of digital, cultural and technological transformation
Interview with Marika Maschietto, controller and strategy manager of Maschietto Elettromeccanica s.r.l.
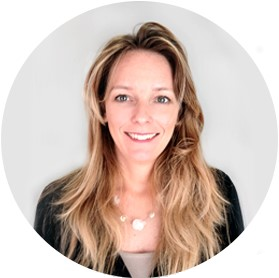
Launching a digital transformation project for a company is a long and obstacle-filled journey that requires a good deal of courage and determination, especially if you want to act along the entire production chain.
However, the results are considerable, some of which are even unexpected, such as a renewed motivation to work and improved corporate well-being of all employees. This is the case of Maschietto Elettromeccanica, a small business in the Pordenone area that has been engaging in the maintenance and repair of electromechanical machines and equipment since 1978 and that, in little more than two years, has undergone a deep change, transforming its production into a real workshop 4.0.
We met Marika Maschietto, controller and head of the company’s organisational strategy, who told us about two complex years, filled with successes and difficulties. The look in her eyes today, however, gleams with satisfaction, being that of someone who knows the hardest time is behind and she can now power ahead.
Q: How did you get in touch with IP4FVG?
It happened in 2018 through LEF, one of the partners of the regional digital innovation hub; we did an assessment, a kind of check-up to gain an insight into our level of corporate digitalisation. Needless to say, we were at year zero. After that, we were supported by the Trieste hub.
Q: What prompted you, what were the most pressing needs?
First of all, we needed to monitor orders; we have many of them, all very different and constantly growing, with a very short lead time. We had to monitor the progress of the job order from entry to testing and plan workshop activities. In addition to this, we needed to prevent our corporate know-how from dissipating; we needed to define procedures and find a way to pass on experiences and skills to newcomers. Basically, operations needed to be standardised. Embarking on a digitalisation journey “forced” us to define key procedures and business know-how more accurately.
Another goal was to be able to provide our customers with test certificates that could attest to the work done and the data on the tests performed. This was a bit of a tall order as the order flow was not tracked accurately and the testing machines were not connected.
Q: Which of these needs did you start with and what kind of technologies did you deploy?
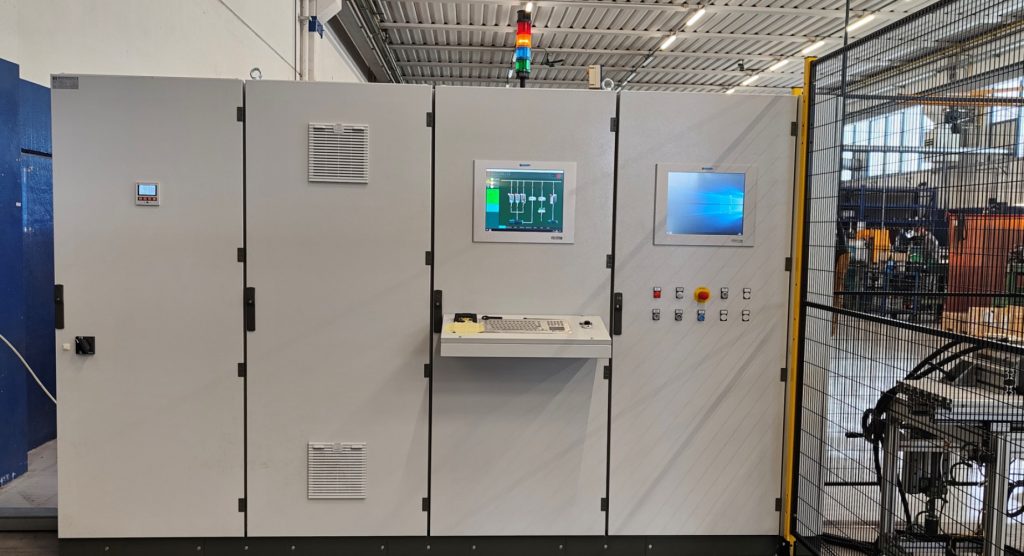
Through the assessment, we identified the way forward: the first thing to be addressed was to improve the organisation of workflows. So we decided to have all employees attend a lean methodology course. It was a very tough time, because productivity had to be maintained at the same time. But we did not have much of a choice: the company had to grow and change its mindset all together.
As a result, we analysed internal flows with a fresh perspective and made the first changes to the physical layout of the workshop. At the same time, we tackled the IT aspect: a thorough analysis of our IT infrastructure revealed that it did not meet modern standards of reliability and availability, so we relied on an external provider who now provides us with a level of service adequate to our needs.
Another step involved changing our CRM. We also needed to integrate an MES for machine control and to improve job order management. Thanks to IP4FVG’s mapping of ICT companies and solutions, we reached out to two possible suppliers that we also assessed by comparing them with others we were acquainted with. Changing our CRM was, perhaps, the most challenging step; it turned out to be a year-long effort. Once rolled out, the new CRM was integrated with the MES.
Q: And from here then a new journey began…
Yes, it was a significant stage that marked the end of this first milestone and the beginning of a new step. Indeed, we have completed the construction of a test bench for brushless motors, which will soon be integrated with the MES. This will allow order-related data to be fed into the CRM and sent to the system. The bench was made to our design and will allow testing to be performed on all brushless motors, regardless of model or brand. Based on the same philosophy of integration with company CRMs, we then completed the revamping of balancing machines, which will soon be integrated and communicating with the entire workshop. The ultimate goal is to obtain different test certificates based on the machines being repaired.
Q: Despite a complex path, what are the main benefits you have achieved?
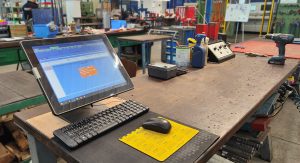
At present, we can say that we have a more stable IT infrastructure: we have secured business data and know-how, thanks in part to choosing the right partner for us.
Our new CRM will also enable us to better develop our customer services and monitor progress from acceptance to final testing and billing. This allows us to increase our quality standards and gain a stronger foothold on the market, because it identifies us as a reliable company.
Another equally important aspect is the improvement in well-being at work. There is less chaos in the company in terms of order and workshop management, staff have improved their skills and are more at ease and motivated. In addition, the company has also become more attractive for the new resources we want to hire, because it is innovative and in step with the times.
Q: What role has IP4FVG played and how has it supported you on this journey?
Initially, the assessment provided us with an road map of steps to be taken. We were able to carry out the activities we had planned and scheduled thanks to the grants we obtained as a result of our participating in innovation calls promoted by the FVG Region and the MISE.
However, I am not sure we could have embarked on this journey without IP4FVG. It has been a fellow traveller, a guide with whom to share choices and doubts. Knowing that we could count on selfless and free support allowed us to trust them completely as we were aware that any suggestions would be objective. We never felt alone, even in the most difficult times. And believe me, there have been quite a few. But now we are more than satisfied! From here on, we can only power ahead!