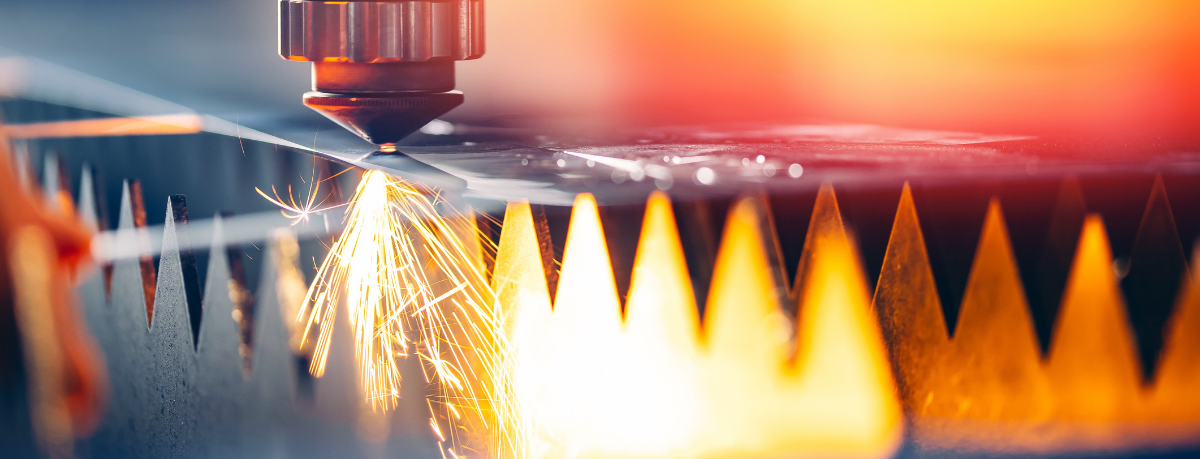
5 Aprile 2022
L’Internet of Things alleato dell’energy saving nelle industrie manifatturiere
Il caro energia degli ultimi mesi sta creando difficoltà a molte aziende manifatturiere, che nel peggiore dei casi si trovano a dover fermare la produzione per l’aumento considerevole dei costi.
Mai come adesso l’efficienza energetica non è solo volano di innovazione (l’implementazione di sistemi ad alto contenuto tecnologico permette il risparmio energetico che libera risorse aziendali, impiegabili in attività R&D), ma permette un aumento significativo della competitività.
L’Internet of Things (IoT) è in grado di migliorare le prestazioni energetiche in particolare in due ambiti: il monitoraggio delle condizioni indoor per l’efficienza di climatizzazione e il monitoraggio elettrico delle diverse linee di produzione per Key Performance Indicators.
Un caso studio esemplificativo è quello che ci ha illustrato Francesco Artuso, ingegnere della Business Unit Energy Efficiency di Eurix, azienda torinese di consulenza informatica orientata alla progettazione e alla realizzazione di soluzioni software.
L’intervento è stato realizzato nello stabilimento produttivo (45.000 mq) di un’azienda metalmeccanica in provincia di Torino, con aree di produzione e magazzino, 3 turni di lavorazione e consumi di circa 500.000 mc/anno gas naturale, di cui il 75% impiegati per la climatizzazione.
Il primo intervento è relativo all’efficientamento energetico del sistema di climatizzazione, basato su rete di sensori IoT. Sono state utilizzate diverse tecnologie, quali sensori di temperatura, umidità relativa, CO2 con tecnologia radio e gateway IoT, controllori dell’impianto di termoventilazione con a bordo algoritmi di Energy Intelligence in sinergia con i sensori, un Building Management System per la gestione e il controllo remoto del sistema oltre all’integrazione di contatori dell’energia termica. Ciò ha permesso di ridurre il consumo termico del 25%, grazie alla regolazione intelligente basata su sensori IoT collegati alle previsioni metereologiche. La gestione centralizzata e automatica di più sottostazioni, inoltre, ha portato ad un minor numero di interventi umani e alla consecutiva riduzione dei costi di sicurezza.
Il secondo intervento ha visto invece l’utilizzo di sensoristica IoT per il monitoraggio elettrico sulle linee di produzione. In questo caso sono state utilizzate tecnologie, come lo Smart Datalogger per le misurazioni delle grandezze elettriche su linee trifase, un database in Cloud per la storicizzazione dei dati, tool di data visualization avanzata per l’analisi dei Key Performance Indicators e algoritmi di Machine Learning per il rilevamento di anomalie e per la manutenzione predittiva.
Tutto ciò ha permesso la definizione delle priorità di intervento sulle linee di lavorazione in base a criteri di efficienza energetica e di produttività. Gli algoritmi di rilevamento delle anomalie e la manutenzione predittiva hanno aumentato del 5% la disponibilità delle linee di produzione e ridotto del 12% i giorni/uomo impegnati per la manutenzione.
Ma qual è il primo passo per avvicinarsi a investimenti di questo tipo? La prima cosa da fare è analizzare in dettaglio caso per caso.
Samuele Giacometti, referente dell’Agenzia per l’Energia del Friuli-Venezia Giulia (APE FVG) per il settore termomeccanico, ci ha raccontato lo sviluppo di un nuovo tipo di audit energetico grazie all’esperienza acquisita nell’ambito di CAESAR, progetto EUSALP che ha avuto l’obiettivo di promuovere fra le PMI dell’Arco Alpino i temi dell’efficienza energetica e l’uso di fonti rinnovabili. Insieme a Toyota Material Handling Italia, APE FVG ha eseguito alcuni audit presso imprese del territorio regionale, nel corso dei quali veniva associato al tema dell’efficienza energetica quello della efficienza produttiva, secondo un approccio di Lean Transformation. Il nuovo metodo “SOLE” (Sostenibile, Olistico, Lean, Efficace) ha come obiettivo quello di accompagnare le PMI verso la neutralità climatica con un modello di impresa efficiente e competitivo caratterizzato dalle seguenti tappe:
- Audit energetico
- Attuazione delle misure raccomandate
- Miglioramento continuo
- Monitoraggio nel tempo dei risultati che queste producono.
Obiettivo in linea con la call europea “Energy-efficient manufacturing system management”, finalizzata a ridurre in modo sostanziale i consumi energetici dell’industria manifatturiera, che ha finanziato il progetto ECOFACT. Avviato ad ottobre 2020, si pone l’obiettivo di realizzare una piattaforma eco-innovativa di gestione energetica per l’industria basata su una migliore dinamica sia in termini LCA (analisi del ciclo di vita) e LCCA (costo del ciclo di vita) verso la sostenibilità olistica della produzione.
L’adozione e combinazione di soluzioni di Digital Twin, big data analytics, Internet of Things, tecnologie cloud e intelligenza artificiale permetteranno di innovare il controllo del consumo e del costo dell’energia nella manifattura agendo in modo proattivo su base previsionale. La scadenza è prevista a settembre 2024.